INTRODUCTION
Layered α-zirconium phosphate Zr(HPO4)2·H2O, abbreviated as α-ZrP is a typical artificial cationic layer compound material.
The structure is layered, with each layer consisting of planes of zirconium atoms bridged through phosphate groups which alternate above and below the metal atom planes.
α-Zirconium phosphate has properties useful for ion exchange, adsorption, catalysis, etc.
α-Zirconium phosphate has both high thermal and chemical stability and these properties make α-ZrP a promising candidate material for many technological applications.
Recent studies indicate that the addition of α-ZrP to lubricating oil can increase the maximum non-seizure load (PB) of the base oil from 470 to 598 N and decrease the wear scar diameter (WSD) of the base oil from 0.58 to 0.33 mm; also,this additive which is shown to have anti-wear capabilities superior to those of MoS2 and graphite additives.
α-ZrP and α-Na2Si2O5 exhibited synergistic behaviour as lubricant additives in mineral oil. The wear scar diameter and the friction coefficient of the combination (α-ZrP: α-Na2Si2O5 mass ratio 1:3) can reach 0.27 mm and 0.110, respectively. The lubricating properties of the combination are superior to α-ZrP and α-Na2Si2O5 alone.
A four-ball machine is used to evaluate α-ZrP as an additive in lithium grease. The results obtained for various amounts of additive are compared with those obtained with the MoS2 additive.
The action mechanism is estimated through analysis of the worn surface with scanning electron microscopy (SEM) and energy dispersive spectra (EDS).
EXPERIMENTAL
Preparation and characterization of α-ZrP:α-ZrP exhibited a good lubricating property
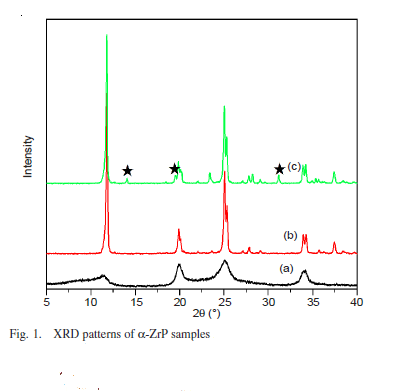

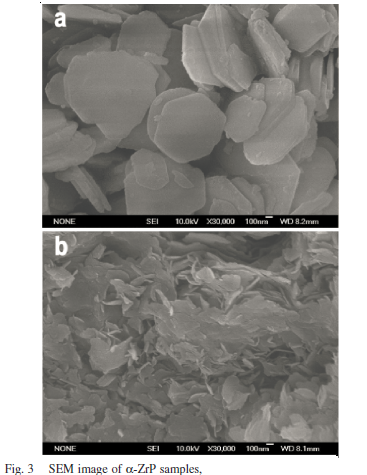
Friction and wear tests:
The anti-wear property, friction reduction property and load-carrying capacity of the as-prepared lithium grease were evaluated on a four-ball tester (a point contact test).
The friction and wear tests were conducted at 75 °C, with a rotating speed of 1450 rpm, loads of 196, 294, 392, 490, 588 and 686 N and a test duration of 0.5 h. The weld point and maximum non-seizure loads were determined according to the national standard method SH/T 0202-92 which is similar to ASTM D2596-1997. The balls (diameter 12.7 mm, HRc 59-61) were made of GCr15 bearing steel (AISI-52100).
The wear scar diameters on the three lower balls were measured using an optical microscope to an accuracy of ± 0.01 mm and the friction coefficients were recorded automatically with a strain gauge.
Three identical tests were performed to determine an average so as to minimize data scattering. SEM and EDS were employed to analyze the rubbing surface.
RESULTS AND DISCUSSION
Tribological properties of α-ZrP:
The present study investigates the tribological properties of α-ZrP as grease additive and compares it with those of MoS2. Fig. 4 displays the variation of the wear scar diameters with the concentration of additives under a load of 294 N and the variation of the PB values with the concentration of additives. The wear scar diameters of the lithium grease containing α-ZrP are much lower than those containing of MoS2 at all concentrations.
The wear scar diameter of α-ZrP at first decreases from 0.50 mm (the wear scar diameter of the base lithium grease) to 0.30 mm quickly as the additive concentration increases from 0.5 to 3.0 wt. % and the wear scar diameter increases to 0.36 mm when the concentration increases to 4.0 wt. %. The wear scar diameter of MoS2 decreases slowly from 0.50 to 0.46 mm when the additive concentration increases from 0.5 to 3.0 wt. % and then increases to 0.56 mm when the MoS2 concentration reaches 4.0 wt. %. Compared to MoS2, α-ZrP performs better with respect to anti-wear. Meanwhile, the PB value of the lithium grease jumps from 353 to 1235 N when the additive concentration of α-ZrP jumps from 0 to 4.0 wt. %.The PB values of the lithium grease go up slowly from 353 to 617 N when the additive concentration of MoS2 increases from 0 to 4.0 wt. %, affording lower PB values than those of α-ZrP.
These results show that α-ZrP has excellent load-carrying capacity. According to the above (that is, minimum wear scar diameter values were obtained at additive concentration of 3.0 wt. % and PB values increased slowly from 3.0 to 4.0 wt. %),the optimum concentration of the α-ZrP and MoS2 as additives in lithium grease is around 3.0 wt. %.
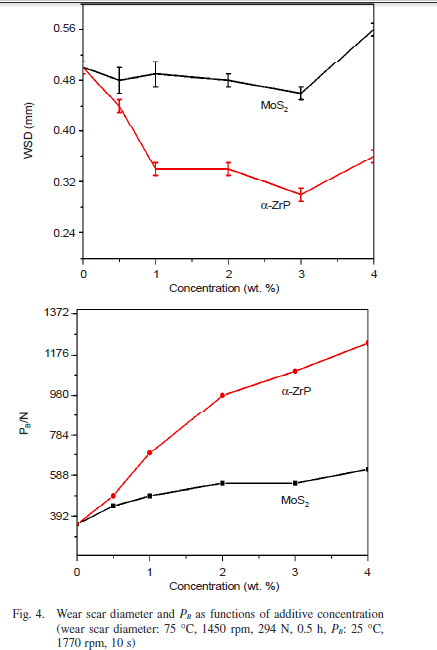
Fig. 5 shows the relationship between the friction coefficient and the applied loads with the lubrication of lithium grease containing the two additives.
As an additive, α-ZrP was found to considerably decrease the friction coefficient from 0.102 to 0.058 as the applied load increases from 98 to 686 N. With regard to MoS2, the friction coefficient decreases gradually with applied loads ranging from 98 to 294 N and then the wear test was interrupted when the applied load increased to 392 N. This is because the MS-10J four-ball tester has automatic protection settings when the friction coefficient reaches a value of 0.2 (severe wear). The friction coefficient trends of base lithium grease are similar to grease with MoS2.
The results of the friction coefficient demonstrate that α-ZrP is an effective additive in improving the friction-reduction properties of lithium grease.
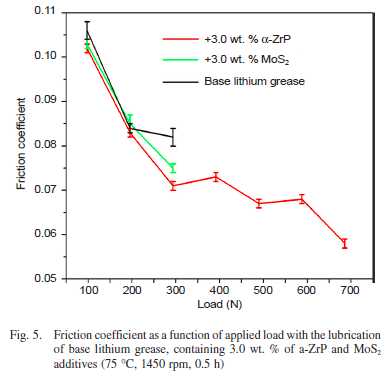
From Fig. 6, it can be observed that wear scar diameter of α-ZrP at first gently undulates from 0.28 to 0.30 mm as the applied load increases from 98 to 294 N and the wear scar diameter values increase from 0.37 to 0.41 mm when the applied load rises from 392 to 686 N. For MoS2, the wear scar diameter values fluctuate a little in the range of 0.43 to 0.46mm as the applied load increases from 98 to 294 N.
In contrast, the wear scar diameter of base lithium grease goes up almost linearly from 0.35 to 0.50 mm. Considering that the wear scar diameter values in the whole range of applied loads, asprepared α-ZrP performs the best with respect to anti-wear.This also suggests that α-ZrP has a high load-carrying ability in the relative long-time run wear test.
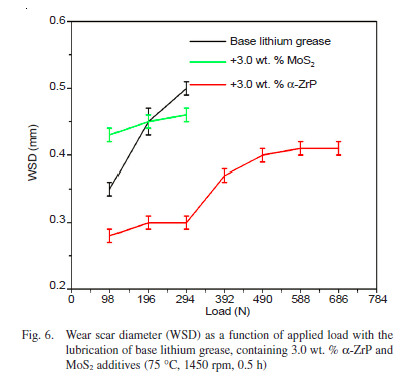
Scanning electron microscope and energy dispersive
spectra analysis of rubbing surfaces:
Scanning electron microscope (SEM) and energy dispersive spectra (EDS) analysis were employed to observe the rubbing surface of thelower steel balls after testing with the base lithium grease, lithium grease with 3.0 wt. % MoS2 and lithium grease with 3.0 wt. % α-ZrP and the results are presented in Fig. 7.
Under a load of 294 N, the worn surface lubricated by the base lithium grease and 3.0 wt. % MoS2 lithium grease were seriously damaged with deep furrows on the rubbing surface. On the other hand, steel balls lubricated by 3.0 wt. % α-ZrP grease exhibited a relatively shallow wear scar. This is consistent with previously measured wear scar diameter results in Fig. 4 and 6 (base lithium grease: 0.50 mm; lithium grease with 3.0 wt. % MoS2: 0.46 mm; lithium grease with 3.0 wt. % α-ZrP: 0.30mm). As the load increased to 686 N, the wear scar diameter of the 3.0 wt. % α-ZrP grease only reached about 0.41 mm with some deposits spread out on top of the wear surface .
The element composition of the rubbing surface lubricated by base lithium grease, lithium grease with 3.0 wt. % MoS2 and lithium grease with 3.0 wt.% α-ZrP were analyzed by EDS and the results are showed in the left column of Fig. 7. It can be seen that there is no other element except those of the friction pair itself (C, Fe and Cr) on the rubbing surface of the friction pair lubricated by both the base lithium grease andthe lithium grease with 3.0 wt. % MoS2, while there are Zr, Pand O on the rubbing surface besides Fe, Cr and C after using α-ZrP as an additive in lithium grease. It is known that the purpose of lubrication is to form films that have high load carrying capacities and low shear strengths, so as to reduce the friction resistance and decrease the wear of the friction pair. Obviously, α-ZrP grease can form a protective film and the solid protective film provides for further reduction of the friction and wear of the contacting pairs and thereby increases their load carrying capacity and anti-wear property compared to the base lithium grease and the lithium grease with MoS2.
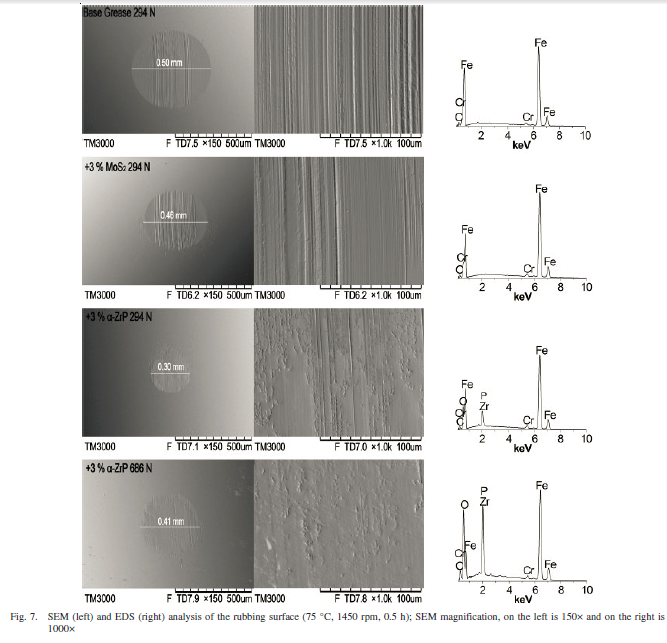
Conclusions
To summarize the present work, the following conclusions are drawn:
• α-ZrP with high crystallinity, uniform diameter and regular morphological forms.
• The tribological test showed that the anti-wear property of α-ZrP as an additive in lithium grease depends on the additive concentration.
• The optimal concentration of α-ZrP is 3.0 wt. %, which exhibits excellent anti-wear, load-carrying and frictionreducing properties. α-ZrP displayed a better lubricating property than MoS2.
• SEM and EDS analysis indicate that α-ZrP may form a protective film composed of the elements (Zr, P, Fe, Cr, O, C) on the rubbing surface protecting the friction pairs from wear.