Zirconium phosphate (ZrP) has been investigated as a filler material for fuel cell membranes as it is a good proton conductor that is chemically and thermally
stable.
Preparation of ZrP/ZrO2 nanofibres and the Aquivion™/ZrP composite membranes
Composite membranes of ZrP/ZrO2 nanofibres and Aquivion™ were fabricated by mixing the appropriate quantity of ZrP/ZrO2 nanofibres in a 5% dispersion of Aquivion™in 1-propanol. The mixture was then sonicated until a homogeneous dispersion is obtained, and cast using the doctor blade method. The cast membrane was then dried at room temperature overnight before thermal treatment at 160 ℃ for 1 hour.
A method based on coaxial electrospinning whereby the shell and core solutions contain the sources of phosphorus and zirconium respectively, resulting in a ‘reactive’ electrospinning where ZrP is formed in situ during fibre formation.
Characterisation of ZrP/ZrO2 nanofibres and the Aquivion™/ZrP composite membranes
1.SEM images and fifibre size distribution of electrospun ZrP fifibres (prior to calcination) spun using a Zr propionate : P2O5 mass ratio of 4:1 (which was kept constant by modifying the sheath solution flow rate) and a sheath solution concentration of 5% and 10% w/v P2O5.
2.Fibre size distribution of distribution of electrospun ZrP fifibres before and after calcination; fifibres were electrospun using a Zr propionate: P2O5 mass ratio of 4 : 1 and a sheath solution concentration of 10% w/v P2O5.
3.TEM cross-section micrograph of the ZrP/ZrO2 fibres.
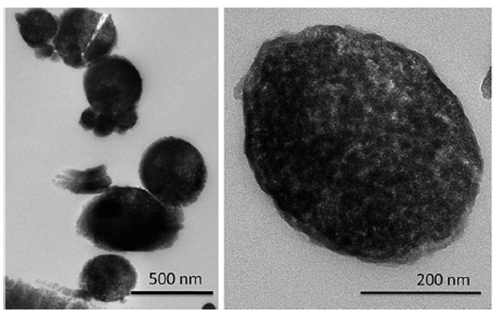
4.HRTEM EDS analysis of the Zr and P content of the centre and the surface of the ZrP/ZrO2 fibres cross-section.
5.Solid state MAS31P NMR spectra of the ZrP nanofibres: as electrospun, after calcination, and after treatment with H3PO4.
6.Proton conductivity measurement of the composite membranes compared to reference membranes.
7.Mechanical properties
8.Mechanical stress–strain measurement of the composite membranes at (a) ambient temperature and RH and (b) 70 ℃ and 80% RH.
Conclusions
Zirconium phosphate/zirconium oxide composite fibres have been prepared by electrospinning using a novel, reactive coaxial electrospinning approach where a coaxial needle was used to prevent premature mixing and gelation of the reactants.
The use of a coaxial needle to separate the solutions of the zirconium precursor and the phosphorus source prevents gelation due to the formation of ZrP gel and enables fibre formation. Calcination and H3PO4 treatment of these fibres yield the ZrP/ZrO2 nanofibres, the formation of which was confirmed using 31P NMR.
The fibre morphology is dependent on solution parameters such as the concentration of the phosphorus source, which suggests that the fibre diameter is dependent on the gelling time of the solution. Cross-section HRTEM EDS shows equal concentration of phosphorus on the edge and centre of the fibres, indicating that its formation was sufficiently rapid,resulting in an amorphous rather than a core–shell morphology. Incorporation of the nano fibres into Aquivion™(a short-side chain perfluorosulfonic acid) membranes resulted in increased mechanical properties with greater elastic modulus and yield point as well as increased proton conductivity compared to both cast and commercial Aquivion™ membranes, showing the potential of such a nanofibre reinforced membrane in fuel cell applications.
(Article in·DOI: 10.1039/C4TA01383B)